It’s a simple fact of life that a CNC’ed Sherline mill requires a counterweight pulling the head upward, because, without some help, that poor little Z-axis motor has a hard time lifting the head’s nine-pound dead weight. The fact that it’s cantilevered way out from the Z-axis dovetails is another problem: there’s plenty of torque binding those ways.
For the last few years I’ve hung a random hunk of iron from a pair of pulleys attached to the floor joists overhead, but that’s not portable and I’m planning to bring the mill to the Cabin Fever Expo again this year. So I hacked out a sort of gantry that works reasonably well and, when I get back, it’ll replace my crude pulley lashup on the joists.

The main beam is an aluminum extrusion that looks like it started life as a traffic sign post; it came with the house and Ol’ Gene was tight with the town DPW, so that seems reasonable. The center support is actually a pipe clamp that I’ll crunch on the edge of the table at the expo, with two plywood scraps to keep from embossing their furniture: the pipe sticks straight up from the table.
There’s an expanding plug inside the top of the pipe that I must go into more detail about later, but the general notion is that the beam becomes one with the pipe when I crank on the nut. I faced off the top of the pipe and cleaned out the graunched metal at the end of the threads.
The gray strap should hold electrical conduit to a wall, yet fits perfectly on iron pipe; who knew? Given that no plumbing size matches any physical property you can actually measure, specifying a match like that is impossible.

I made a pair of pulleys around 26 mm OD ball bearings, mostly because I couldn’t find anything else that would work. Yes, they’re open to shop crud, but I’ll add side shields before I screw it to the ceiling. I know I’ll be explaining how they work at Cabin Fever, so there’s no point in hiding the things.
The shaft is a steel rod, turned to fit and drilled out for a 10-32 screw. The greenish dab on the shaft is Loctite; I slid the pulley over the dab, aligned the cable with the hole, and let it cure in place. Loctite gets me out of making a quartet of fussy little spacers: better living through chemistry.
The outer ring is polycarbonate, chosen because the sheet was the right thickness. This ought to be a lathe project, but it was easier to clamp it on the mill, so I helix-milled the center hole to fit the bearing OD.

I hammered a piece of copper pipe into a mandrel / jaw pad, put a thin chunk of acrylic under the polycarb as a spacer, grabbed the whole affair in the three-jaw chuck, and helix-milled the OD. No drive dog to hold it in place, no special prep, no nothing: it Just Worked. Of course, I’m taking sissy little cuts on the thing, but you best do that on a Sherline anyway.
The copper pipe mandrel trick doesn’t give great precision, which, fortunately, isn’t needed in this application. I found a chunk of EMT in the heap with the right OD and walloped the copper pipe around it with a rubber mallet to beat it into shape.
The reason you need a mandrel is that thin ring of plastic deforms under the pressure of the jaws, producing a three-lobed effect: pleasing in an art project, yet strangely inappropriate in a nominally circular machined part. I discovered this exquisite little inconvenience a few years ago and haven’t forgotten the lesson yet.
I planned to use a slitting saw to cut a groove for the wire rope around the OD, but then I came to my senses: ‘way too much leverage on that poor little chuck and not enough traction from the jaws. A bit of rummaging came up with a 3/16-inch ball-end mill burr, which was just slightly larger than the wire rope.
[Update: What I’ve been calling a “ball-end mill” is actually a “ball-end burr”. A “ball-end” or “ball-nose” mill is basically an end mill with a hemispherical end. Sometimes “burr” is spelled “bur”.]

Then I screwed up: I mounted the chuck on the rotary table, the table on a right-angle plate, the plate on the mill, and zeroed the ball at the top of the pulley.
The right way to use a ball-end mill burr is along its equator, so I should have zeroed it at either the left or right side of the pulley. The ball doesn’t have really great cutting edges around its South Pole.
Fortunately, it cut a 1.5-mm trench around the polycarb just fine. I suspect if I was using aluminum, this would not have had a happy outcome.
The parts heap yielded a pair of lead blocks, a sturdy eye screw, and some humongous heat-shrink tubing that made a tidy counterweight. I lashed everything to the countertop supporting the mill, added a 2×4 post and a machinist’s jack to support the countertop, and it passed the smoke test.
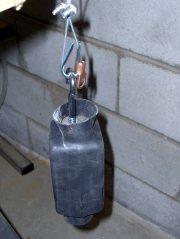
The Sherline seems happier with a counterweight that slightly outweighs its head. The lead blocks weigh 13 pounds, about 3 pounds more than the head, and Z-axis travel is nice & smooth.
It’s said that the disadvantage of removing all the weight from the head is that there’s less weight to press drill bits into the workpiece. I haven’t seen that problem yet; methinks a few pounds really don’t make that much difference compared to the forces generated by the motor through the leadscrew. We shall see when this thing is installed in its permanent home on the floor joists.

Real machinists make all sorts of lavish clamps to attach the counterweight rope to the Sherline mill head. I favor the Orc Engineering approach: a random hook from the heap, firmly attached with a big hose clamp, more-or-less over the head’s center of mass. What’s not to like?
Incidentally, one nice feature of a hook on the head is that you can hang the head out of the way under a nearby shelf. I have both the 3k rpm and 10k rpm heads and it’s really nice to have the other head conveniently located, yet out of the way.
Something that’s obvious in retrospect: that pipe’s gotta be very close to vertical, lest the cable drag on the side of the holes. I may need some shims on the Cabin Fever table to make the answer come out right.
Here’s the heart of the helical-milling rough-cut routine for the OD. We start at a safe Z-axis traverse level and the first pass is at Z=0 on the surface to reveal any gross alignment errors…
G0 X[0 - #<_Pulley_Radius>] Y0 (set up for cutter comp) G41.1 D[#<_Tool_Dia> + #<_Cut_Finish>] (cutter comp on left) G2 X[#<_Pulley_Radius>] I[#<_Pulley_Radius>] F#<_Traverse_Feed> (CW entry arc to right side) G0 Z0 F[#<_Mill_Feed> / 2] #<_Pass> = 0 (iteration counter) #<_ZLevel> = 0 (current Z-axis level) O100 DO G2 X[#<_Pulley_Radius>] I[0 - #<_Pulley_Radius>] Z#<_ZLevel> (helix down) #<_ZLevel> = [#<_ZLevel> - #<_Cut_Depth>] #<_Pass> = [#<_Pass> + 1] O100 WHILE [#<_Pass> LE #<_Num_Passes>] G2 X[#<_Pulley_Radius>] I[0 - #<_Pulley_Radius>] (remove ramp to final level) G40 (comp off) G0 X#<_Pulley_Dia> Y0 (move away from part) G0 Z[#5163 * 25.4] (get air)
Memo to self: use the ball mill’s equator next time.
Update: The thing fit perfectly on the floor joists over the mill; more info there.
The first conduit was the existing black iron pipe used to supply illuminating gas to the gaslights; when this new-fangled electricity stuff came along, it turned out you still wanted to put your lights in the same place, and the gas pipe made a handy place to stick the wiring. And the rest, as they say, is history — and all the newfangled conduit had to be backwards compatible with the oldfangled conduit, of course.
And copper pipe sizes came from the iron pipe ID that produced an equivalent flow or something like that… made perfect sense at the time, I’m absolutely sure!